Back To Buyer's Guide
What is Lamination?
Lamination is the process of sealing a document (id card, letter, certificate, photograph, poster) or fabric between two layers of plastic film (one layer for single sided lamination). An extended version of laminating call "over laminating", is the process of mounting a laminated item to a "substrate" (stiff foam board, wood or metal backing) overlaid with laminating film.
Thermal or heat activated laminating films are constructed of a layer of polyester base film and a layer of adhesive resin, bonded together. During the lamination process, the adhesive resin is softened or liquefied and permanently bonded to the document. Once liquefied, the adhesive is spread across the surface and with pressure, bonded to the surface of the document. The adhesive then hardens as it cools creating a permanent bond between paper and film.
There are several types of laminating machines that provide different methods of adhering film. More on this topic is discussed under "Choosing the right Laminator". General laminating requires the document to be fed into the laminator where it contacts the film adhesive. The film is then pressed into the document with a set of rollers or a large plate. The laminate film and document are now one, protecting the document from the elements while enhancing its visual appearance.
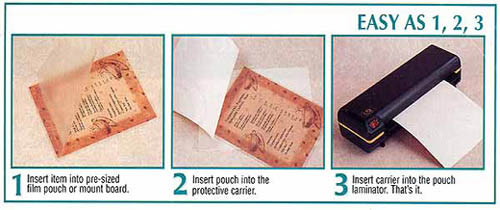
Choosing the Right Laminator
Identifying the correct laminator of any application is an easy task. You need to consider several factors.
Hot Lamination
Pouch
Pouch Laminators are compact tabletop units designed for laminating documents up to 20" wide. Theses machines are ideally suited for creating ID Badges, protecting photographs, making small window displays or sealing certificates. Depending on the task, pouch laminators are available in two, four or six roller configurations. The more rollers, the higher the production capability and quality of the lamination. Pouch Laminators are the cheapest of the laminators starting at around $80. Although they start fairly inexpensive, there are many high quality heavy-duty pouch laminators that cost up to $600.
Roll
Roll Laminators are designed for laminating larger documents up to 60 inches wide (wide format) and one inch thick. Machines are available ranging from single event use to moderate office applications to commercial grade units running continuous 1000' rolls of laminating film in high production environments. To accommodate larger sizes, higher production rates and provide a quality end product, roll laminators include advanced process control features like Variable Speed, Temperature Control Adjustment, Reverse Roll, Pressure Adjustment, Slitters and Cooling Fans. In addition to hot lamination, over-laminating, cold film mounting and substrate mounting processes are possible with large roll laminators.
The document is fed into the laminator on a feed tray. Where it meets the film is called the "nip". The adhesive in the film has already been activated with heat by either a "heat shoe" or a heated roller. In the "nip" the film is pressed into the document with the first set of rollers. It then passes to the second set of rollers, called "finishing rollers". Roll Laminators are amongst the more expensive laminators. They start at around $1,000 and are as much as $5,000. There are some industrial models that can reach up to $10,000+.
Dry Mount
Dry mount laminators use a tissue adhesive, calculated heat, pressure settings and time to apply a substrate to a document. The tissue (adhesive) is inserted between the document and substrate. It is then placed in the press where a pre-determined temperature has been set. It is pressed for a specific time period as the adhesive is heated and forced into both the document and substrate, thus adhering them together. If the pre-determined time has been fulfilled and a strong bond has not occurred, the document may be pressed again. Additional "pressing" does not cause damage to either substrate. Dry mount presses vary in price from $1,500 to $6,000.
Cold Lamination
Tape
Tape Lamination is the process of "sandwiching" a document between two layers of film with pressure. The film's adhesive is already in a "tacky" state. The tape (both top and bottom) is contained in pre-wound roll cartridges that simply pop in to the laminator. The document and laminate are pulled through the two pressure rollers by the rollers themselves. This is achieved by a manual hand crank or a push button.
Tape Laminators require no electricity, instead employing an innovative replaceable tape cartridge system. Tape Laminators transfer pressure tape or film to flat material or PSA over-laminate to finished materials (signs or promotional items). Designed primarily for sign and graphics applications, Tape Laminators are typically used in sign shops, photo-finishing labs, reprographics shops and manufacturing plants. Available in either electric or manually operated roller models, tape laminators are efficient and easy to use machines. Tape laminators are also fairly inexpensive starting around $150.
About Laminating Film
Laminating film is defined by size and thickness. Film size is determined by application from 2.25" X 3.75" business card dimensions up to 60" wide by one-thousand foot long rolls for high production wide format applications. Thickness (or Mil) determines how well documents will be protected. ID Badges for example require high Mil values while large graphics arts material requires lower Mil values for clarity and because large items are handled less frequently than small badges.
For effect and protective qualities, laminating films are available in many finishes.
The Weight or thickness of lamination film is expressed in mils. Lamination pouches are 1.5, 3, 5, 7, 10 or 15 mil thick. The higher the mil number, the thicker the film. The mil weight is expressed per side; therefore, the total weight of the film has to be doubled. Example: A 3 mil pouch has two sheets of 3 mil film plus your document (regular bond paper is 4 mil) for a total aggregate of 10 mil.
Laminating Defects
Clouding and "orange peel" are two common occurrences in pouch laminating. Clouding is the result of not using enough heat in the lamination process - "orange peel" is the result of too much heat. By following this simple chart you can virtually eliminate clouding and "orange peel".
Foil Stamping
GBC Creative Foils are available for use with select GBC laminators, which add the look and impact of foil stamping to any document, inexpensively. You apply the foil paper over the area you want to add this effect and run it through the laminator. Then when it comes out through the exit tray, peel off the foil paper and the area that had toner based writing will now be foiled. Foils can be applied to any toner-based document from laser printers to copiers. Foils can be applied as a whole sheet or cut to fit over certain areas. Different colors can be used on the same sheet. A carrier is required to prevent foil from getting onto the rollers.
Glossary
What is Lamination?
Lamination is the process of sealing a document (id card, letter, certificate, photograph, poster) or fabric between two layers of plastic film (one layer for single sided lamination). An extended version of laminating call "over laminating", is the process of mounting a laminated item to a "substrate" (stiff foam board, wood or metal backing) overlaid with laminating film.
Thermal or heat activated laminating films are constructed of a layer of polyester base film and a layer of adhesive resin, bonded together. During the lamination process, the adhesive resin is softened or liquefied and permanently bonded to the document. Once liquefied, the adhesive is spread across the surface and with pressure, bonded to the surface of the document. The adhesive then hardens as it cools creating a permanent bond between paper and film.
There are several types of laminating machines that provide different methods of adhering film. More on this topic is discussed under "Choosing the right Laminator". General laminating requires the document to be fed into the laminator where it contacts the film adhesive. The film is then pressed into the document with a set of rollers or a large plate. The laminate film and document are now one, protecting the document from the elements while enhancing its visual appearance.
Choosing the Right Laminator
Identifying the correct laminator of any application is an easy task. You need to consider several factors.
-
What needs to be laminated (paper, fabric, wood)?
If you are using your laminator for mounting, you will probably be laminating thicker items such as wood and foam board in which case you must make sure that your laminator can handle it. You might want to look into purchasing a Dry Mount Laminator or a Pouch laminator with spring loaded rollers to accommodate thicker laminations.
-
What size (credit card, 5x7 photo, 30x24 poster)?
Depending on what you will be laminating, you will have to determine what pouch width is necessary for your purposes. If you just want to laminate ID cards, then a 4" width pouch laminator should suffice. If you want to laminate large items such as posters, you are probably best off with a wide format roll laminator.
-
How many (one or two, dozens, hundreds)?
Do you plan to use your laminator on a daily basis? If there will be a lot of material passing through this machine, you want to make sure that you get a heavy duty laminator. Make sure it is made with steel gears, 4 rollers and metal casing instead of plastic for durability. If your volume is very high, almost constantly running, you might want to get an industrial laminator that can process 20 feet in a minute. You might also be working out of your home office, in which case all you will need is a small pouch laminator.
-
Will the material be laminated on one side, both sides or mounted to a substrate?
You will have to make sure that if you are mounting, your laminator will be able to accept thicker items. Good things to look for are spring-loaded rollers because they automatically adjust to the object's thickness and still apply pressure to the object for great laminations.
-
Where will the laminator be used?
If it is being used in an office for example, it might be helpful to get a laminator with a standby switch so that you can leave it running all day and it will be ready to use at anytime. You might also want to make sure that your laminator has a ready light so that you can see when it is ready to begin laminating.
Hot Lamination
Pouch
Pouch Laminators are compact tabletop units designed for laminating documents up to 20" wide. Theses machines are ideally suited for creating ID Badges, protecting photographs, making small window displays or sealing certificates. Depending on the task, pouch laminators are available in two, four or six roller configurations. The more rollers, the higher the production capability and quality of the lamination. Pouch Laminators are the cheapest of the laminators starting at around $80. Although they start fairly inexpensive, there are many high quality heavy-duty pouch laminators that cost up to $600.
Roll
Roll Laminators are designed for laminating larger documents up to 60 inches wide (wide format) and one inch thick. Machines are available ranging from single event use to moderate office applications to commercial grade units running continuous 1000' rolls of laminating film in high production environments. To accommodate larger sizes, higher production rates and provide a quality end product, roll laminators include advanced process control features like Variable Speed, Temperature Control Adjustment, Reverse Roll, Pressure Adjustment, Slitters and Cooling Fans. In addition to hot lamination, over-laminating, cold film mounting and substrate mounting processes are possible with large roll laminators.
Dry mount laminators use a tissue adhesive, calculated heat, pressure settings and time to apply a substrate to a document. The tissue (adhesive) is inserted between the document and substrate. It is then placed in the press where a pre-determined temperature has been set. It is pressed for a specific time period as the adhesive is heated and forced into both the document and substrate, thus adhering them together. If the pre-determined time has been fulfilled and a strong bond has not occurred, the document may be pressed again. Additional "pressing" does not cause damage to either substrate. Dry mount presses vary in price from $1,500 to $6,000.
Cold Lamination
Tape
Tape Lamination is the process of "sandwiching" a document between two layers of film with pressure. The film's adhesive is already in a "tacky" state. The tape (both top and bottom) is contained in pre-wound roll cartridges that simply pop in to the laminator. The document and laminate are pulled through the two pressure rollers by the rollers themselves. This is achieved by a manual hand crank or a push button.
Tape Laminators require no electricity, instead employing an innovative replaceable tape cartridge system. Tape Laminators transfer pressure tape or film to flat material or PSA over-laminate to finished materials (signs or promotional items). Designed primarily for sign and graphics applications, Tape Laminators are typically used in sign shops, photo-finishing labs, reprographics shops and manufacturing plants. Available in either electric or manually operated roller models, tape laminators are efficient and easy to use machines. Tape laminators are also fairly inexpensive starting around $150.
About Laminating Film
Laminating film is defined by size and thickness. Film size is determined by application from 2.25" X 3.75" business card dimensions up to 60" wide by one-thousand foot long rolls for high production wide format applications. Thickness (or Mil) determines how well documents will be protected. ID Badges for example require high Mil values while large graphics arts material requires lower Mil values for clarity and because large items are handled less frequently than small badges.
For effect and protective qualities, laminating films are available in many finishes.
- Standard Clear (glossy)
- Matte (slightly frosted)
- Satin (de-lustered for reduced glare; not frosted)
- Scratch Resistant (very hard after application)
- Crystal (granular sand like texture)
The Weight or thickness of lamination film is expressed in mils. Lamination pouches are 1.5, 3, 5, 7, 10 or 15 mil thick. The higher the mil number, the thicker the film. The mil weight is expressed per side; therefore, the total weight of the film has to be doubled. Example: A 3 mil pouch has two sheets of 3 mil film plus your document (regular bond paper is 4 mil) for a total aggregate of 10 mil.
Laminating Defects
Clouding and "orange peel" are two common occurrences in pouch laminating. Clouding is the result of not using enough heat in the lamination process - "orange peel" is the result of too much heat. By following this simple chart you can virtually eliminate clouding and "orange peel".
3-mil film | low-med heat | 5-mil film | med heat | 7-mil film | med-high heat | 10-mil film | high heat |
GBC Creative Foils are available for use with select GBC laminators, which add the look and impact of foil stamping to any document, inexpensively. You apply the foil paper over the area you want to add this effect and run it through the laminator. Then when it comes out through the exit tray, peel off the foil paper and the area that had toner based writing will now be foiled. Foils can be applied to any toner-based document from laser printers to copiers. Foils can be applied as a whole sheet or cut to fit over certain areas. Different colors can be used on the same sheet. A carrier is required to prevent foil from getting onto the rollers.
Glossary
- Adjustable Temperature Control: Adjustable thermostats allow for the utilization of a broader range of film thickness and lamination substrates. Adjustable dial thermostat allows for unlimited temperature adjustments over a broad range, ensuring the exact heat setting required for your application.
- Carriers: A folded piece of cardboard with a non-stick coating on one side (glossy side), that is used to protect the laminator. It works by catching any excess adhesive that may squeeze out the sides of the pouch during the heat and pressure process. It keeps the excess adhesive from getting on the laminator rollers and reducing its overall life span and performance. The carrier can also aid in the lamination process by keeping the heat uniform as well as creating added pressure to the document for a more crisp laminate.
- Clouding: Lamination defect that is the result of not using enough heat in the lamination process.
- Cooling Fans: State-of-the-art roll laminators feature cooling fans located at the back of the machine. These fans transfer heat from the document and vent it into the surrounding air to rapidly cool the lamination. Laminations that cool rapidly upon exit are curl free and will lay flat.
- Cooling Plates: Cooling plates are located on the back end of the unit and absorb the heat coming off the exiting lamination, displacing it into the air. The rapid cooling process allows the document to lay flat providing "curl free" results.
- Cooling Tray: provides a flat surface for exiting lamination to cool down on. As the air cools the lamination evenly, the document lays flat providing "curl free" results.
-
Heat Platens: High wattage silicone bonded heaters provide quick warm-up and uniform heat maintaining the heat platens at the desired laminating temperature.
Heavy Weight Platens/High Wattage Heaters: Heavy weight platens are usually 3-4 times thicker than standard platens. This extra mass prevents rapid heat loss while laminating large size documents, heavier film weights or long production runs.
Light Weight Platens & Heating Tapes: These lower cost components, when laminating larger documents or using heavier film weights, allow the heat platen temperature to fluctuate over a broader range resulting in less than professional results.
-
Heat Shoes: Solid aluminum extruded heat shoes heat up to operating temperatures and melts the adhesive on the film as it is drawn across the shoes.
Heavyweight heat shoes: designed to wrap around the front rollers and provide more heating surface. The more heating surface, the longer dwell time as the film moves across the heat shoes. Heat shoes that wrap around the front rollers efficiently heat the rollers for a better, more professional lamination.
Lightweight heat shoes: do not retain heat as well as heavyweight shoes. Large heat shoes provide extra mass to prevent rapid heat loss while laminating heavier films, thicker items or longer production runs.
- Heated Rollers: A heated roller heating system is where the roller itself is heated internally. The heat is then transferred to the document through the roller. This system is closely related to that utilized by some roll laminators.
- Orange Peel: lamination defect that is the result of too much heat in the laminating process.
- Over laminating: The process of mounting a laminated item to a "substrate" (stiff foam board, wood or metal backing) overlaid with laminating film.
- Preset Temperature Control: Less expensive pouch laminators have a preset, non-adjustable temperature setting. These machines typically utilize one sometimes two different film weights.
-
Pressure Adjustment: Adjusts the pressure of the rollers against the lamination to accommodate the thickness of material being laminated.
Laminators with adjustable pressure can be accommodated with either:
Lever Lock type pressure adjustments are pre-set for specific thickness intervals. Simply rotate the lever to the corresponding mark and it locks in place adjusting the pressure accordingly.
Pneumatic type pressure adjustments rely on compressed air pressure to adjust the roller heights to accommodate thin as well as thick substrates up to 1" thick.
Ratchet type pressure adjustments manually spread the heat shoes and roller assemblies to preset stops to laminate substrates up to ??" thick.
- Pressure Sensitive Adhesives: (also called "cold film") require no heat or very limited heat to adhere. PSA film will adhere to almost any substrate and works great for over-laminating and mounting.
-
Pressure Sensitive Take Up Mandrel: an additional mandrel located on the top of a roll laminator directly in front of the upper film supply mandrel. It is designed to peel away the pressure sensitive (cold) film release liner just prior to the film contacting the document. As the mandrel is peeling away the release liner it is also neatly rolling it up for quick and easy discard.
-
Rollers: The most important contributor to finish quality in a pouch laminator. They provide the pressure to your laminate. The highest quality rollers are a combination of metal and an external rubber coating. This rubber allows for greater pressure and smoother finished laminates. Some rollers are coated with silicone, which reduces the risk of adhesive build up.
2 Roller: On a 2 roller machine, you only have the rear rollers that act as both the feed and finishing rollers. Two roller designs are found on the more economical units. When using a two-roller laminator, you must always initially feed the document through the machine at a slow even speed until the rear rollers grab.
4 Roller: On a 4 roller machine, the front two rollers feed the carrier into the laminator at a uniform speed to guarantee even heat distribution. The second set of rollers, called finishing rollers, flattens the film, eliminating wrinkles and curls at the same time applying pressure, forcing the activated adhesive into the document.
-
Reverse Roll: In the event the lamination should wrap-around the rear rollers during the lamination process, the reverse roll feature allows the user to quickly rectify the situation.
Manual: The Manual Reverse feature is a free floating crank that when depressed (the motor must be turned off) and turned will crank the rear rollers around and correct the situation.
Automatic: The automatic reverse allows the experienced user to quickly alleviate the problem with a simple touch of a button.
- Slitters: "Inline trimmer" are used to trim one or both sides of a document as it is being laminated.
-
Spring Loaded Rollers: High-pressure springs are used to force the rollers down flat for perfect edge seal on thin document laminating. When a document mounting board is used, the springs allow the roller to automatically adjust to accept the document while still keeping maximum pressure on the document.
-
Unibody construction: Consists of 2 interlocking halves that are molded for strength and durability. When assembled, the halves lock together into a single unit providing a solid platform in which other components can be built within the machine.
- Variable Speed Control: Eliminates the need to manually adjust the temperature when changing film weights. The user will increase the speed for less heat (Less time contacting the heating element) or decrease the speed for more heat (more time contacting the heating element).